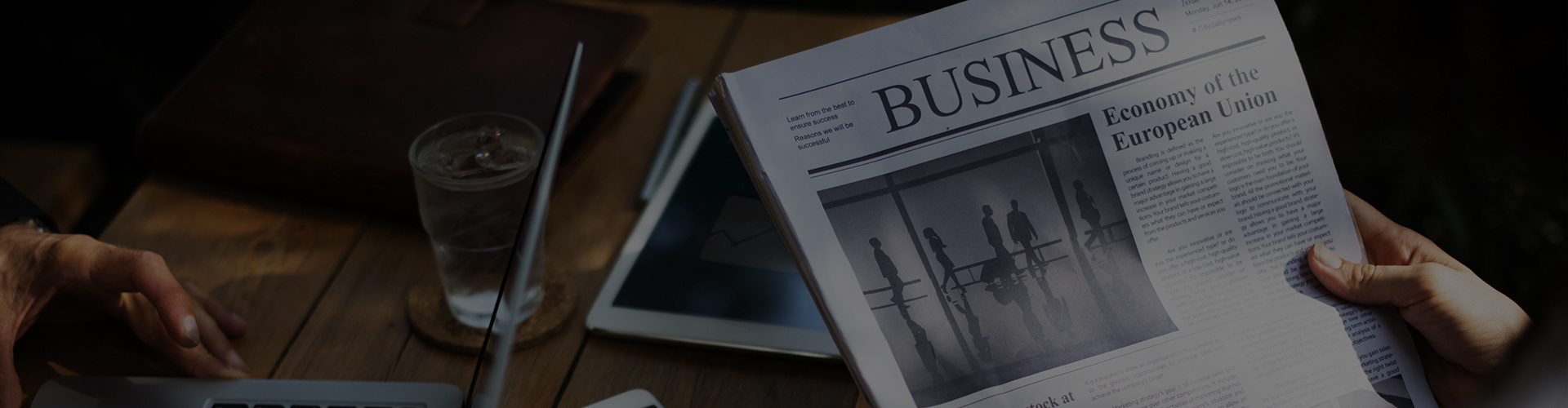
Advantages and disadvantages of different forging processes for metal materials
Time: Nov 18,2022

Forging is defined as the forming or deformation of a metal in its solid state. Many forging is completed by upsetting process. In the upsetting process, the hammer or striker moves horizontally to press on the rod or the end of the rod to widen and change the shape of the end. Parts usually pass through successive stations before reaching the final shape. High strength bolts are "cold headed" in this way. Engine valves are also formed by upsetting.
In drop forging, the part is hammered into the shape of the finished part in the die, which is very similar to the blacksmith's open die forging. In this case, the metal is hammered into the desired shape against the anvil. There is a difference between open die forging and closed die forging. In open die forging, the metal is never completely restrained by the die. In a closed die or die, the forged metal is confined between half dies. Repeated hammering of the die forces the metal into the shape of the die, and the two halves of the die eventually meet. The energy of the hammer can be supplied by steam or pneumatic, mechanical or hydraulic power. In true drop forging, gravity alone pushes the hammer downward, but many systems use power assistance combined with gravity. The hammer provides a series of relatively high speed, low force blows to close the mold.
In pressure forging, high pressure replaces high speed, and the die half is closed in a single stroke usually provided by a power screw or hydraulic cylinder. Hammer forging is usually used to produce smaller parts, while press forging is usually used for mass production and automation. The slow application of press forging tends to process the interior of parts better than hammering, and is often applied to large high-quality parts (such as titanium aircraft bulkheads). Other specialized forging methods vary depending on these basic topics: for example, bearing races and large gear rings are made by a process called rolling ring forging, which produces seamless round parts